1995/08/01
98. zenbakia
eu es fr en cat gl
Aparecerá un contenido traducido automáticamente. ¿Deseas continuar?
Un contenu traduit automatiquement apparaîtra. Voulez-vous continuer?
An automatically translated content item will be displayed. Do you want to continue?
Apareixerà un contingut traduït automàticament. Vols continuar?
Aparecerá un contido traducido automaticamente. ¿Desexas continuar?
CIM Manufacturing Systems
Text created by automatic translator Elia and has not been subsequently revised by translators.
Elia Elhuyar
The CIM (Computer Integrated Manufacturing) manufacturing system incorporates a new production philosophy.
The characteristics and needs of the market have changed radically in recent years, so company planning has had to adapt to survive. Concepts such as quality, flexibility, short delivery times, zero stock are being implemented more strongly. On the other hand, and thanks to the development of computer technology, we have machines to collect and work with many data. The detectors collect and send this data to the computer.
The main feature of the company of the future is its competitiveness: achieving higher quality makes things cheaper and faster. For this it is necessary to have the most advanced equipment (robots, machine tools with numerical control, programmable automatons, manipulators…), but the fundamental concepts are control, automation, integration and communication.
The CIM concept focuses on integration. All steps taken during the manufacturing process are pre-programmed. All data contained in the same database serve to perform different operations: design, production control, planning, accounting, purchasing, quality control, maintenance, etc. Information technology enables the integration of all company activities.
Of course, computer science is essential and whoever sits in front of the general computer has the ability to drive the entire installation and process. He will decide the number of parts to be made, the operation to be used and the operation to be performed and will be able to access at any time all the data and statistics of the system. All this without interrupting the production chain or changing tools or touching anything.
One of the most important advantages of this technology is previous simulation. It can simulate the entire system to avoid collisions, select robots, measure operating time and ultimately improve the system and correct failures.
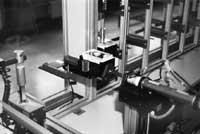
A pneumatic arm carries the part from the conveyor belt to the storage waiting place. Subsequently, another pneumatic arm takes it and stores it in its corresponding place.
The CIM system is composed, among others, of the following instruments:
- Conveyor belt or similar system is used. It serves to transport parts and can be said to be the axis of the CIM system, since all other machines or tools are placed around it. Using the barcode reader or similar detector, the central computer will know where and in what steps of the process each piece is found and then send several commands. The conveyor has the ability to stop one piece while the rest of the parts, including the conveyor itself, continue moving. This allows an operation at this stage on one part, without interfering with the work of all other system components.
- Numerical control milling machine and lathe: are the machine tools used in machining parts. The lathe is ideal to operate cylindrical parts: cylindrical displacement, refractive, conical turning, threading, etc. slope. The capacities of the milling machine are greater, since the parts should not be cylindrical: sacks, paralelepiped squadron, surrounded by irregularly shaped parts, carving straight and circular slots, etc. Numerical control is a programming language that this type of machine tool “understands” automatic machining. This language shows what to do, where to start, where to finish and at what speed the tool will work. Currently numerical control is done by computer (using programs called CAD CAM). In the computer the initial parts are drawn, the machining conditions are established and the final design of the part is determined, and after the numerical control program, the machine to connect the computer to the machine and milling or the lathe will perform the complete work, that is, without the man touching anything else. In addition, and if you have several programs in memory, we can run them automatically, getting great flexibility.
- Robot: is an automatic arm that performs high-precision operations. Its movement is precise and at the same time preprogrammed, able to launch more than one joint, achieving smoother movements. They are often used to transport parts from one place to another, from the conveyor to the lathe, but can also be used to weld, paint and work in environments dangerous to humans in general.
- Pneumatic elements: these are elements that move using the force of compressed air. Compressed air, in addition to being clean and cheap, is able to achieve movements of great precision and speed. It also has its cons: it is noisy and it is not easy to control the speed of movement. Widely used to fit parts, automatic parts feeding, etc.
- Warehouse: is the place where the different parts are stored. Both simple parts and mechanical assemblies after assembly. The pneumatic arm is often used to bring the parts to the warehouse and collect them from the warehouse. The central computer will know at any time the piece in each corner of the warehouse.
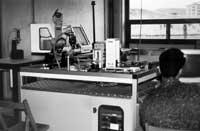
The area of technology and engineering for the automation process is highly developed, but in other areas there is still much to do.
Programmable automaton or PLC: as in general an automaton is used for each control machine, in most cases it will be more than one automaton. In any case, the main PLC will be present in all CIM systems. There are detectors throughout the system that transmit the signal or message to the PLC or main automaton. This reads these input signals and, based on your program, sends commands. Of course, in order to do all this, the whole system needs to be interconnected. A computer could do the same, but the industry uses automatons, cheaper and easier to program. When complexity increases, the computer will be used.
- Software: Software programs are of great importance in this system. In addition, they are many and different: from each machine, communication between systems, design, simulation, management... These include:- CAD-CAM module
(Computer Advanced Design - Computer Advanced Manufacturing). As explained above, it is a module of design and automatic
machining.- CAE module (Computer Advanced Engineering). With this, the influence of external forces after the design of the solid or structure, internal and external stresses, portable temperature, vibrations, magnetic fields, different types of materials, etc. are analyzed in order to know in advance the part, the mechanical assembly or the behavior of the structure.- CAED module
(Computer Advanced Electronic Design). This module consists of the design and simulation of circuits and electronic cards.- CAPP
module (Computer Advanced Processing Planification). You can perform simulation, analysis and planning of industrial operations.
- CACP module (Computer Advanced Control Production). This module works with a database to calculate production control and product cost.
- Rest of the sections: I will not mention them but I do know them.
The area of technology and engineering for the automation process is very developed, but in other areas (logistics, planning, management...) there is still much to do. As it progresses, its impact will be evident in all sectors.
A CIM system not only works for production, but also for research, such as studying the behavior of new tool materials. The flexibility and simulation capability is the perfect tool to perform all tests and analyses before a product comes to market.
It is not easy to implement a CIM system. This technology is known but is only being used in some multinationals. On the one hand, a lot of investment must be made and on the other, the installation of this type of equipment changes the organizational chart and mentality of the company. Loss of jobs and recycling of remaining staff. All of this has important social and economic consequences. Therefore, sometimes “mixed” systems are placed, that is, some operator is interposed during the process. However, the advantages are evident: information orientation, cost control, flexibility, greater dedication to the changes that occur, etc. We cannot lose the train of development. The CIM is undoubtedly a technology of current production and especially of future.
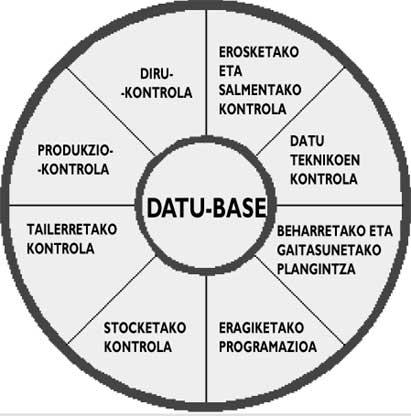
CIM manufacturing system software.